Tinius Olsen
Automated System Cell
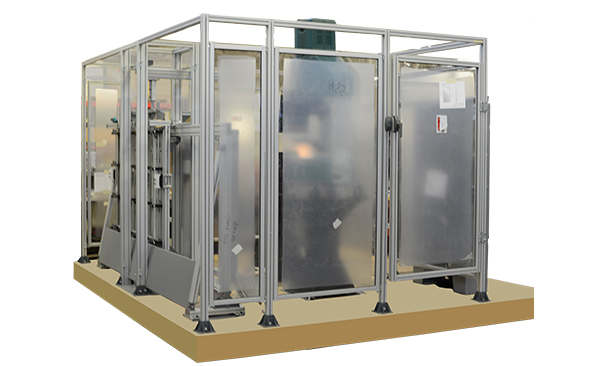
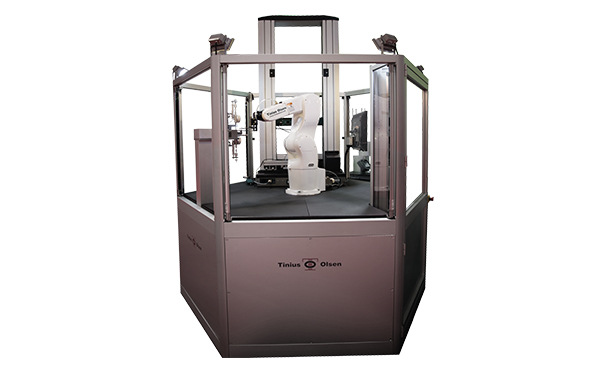
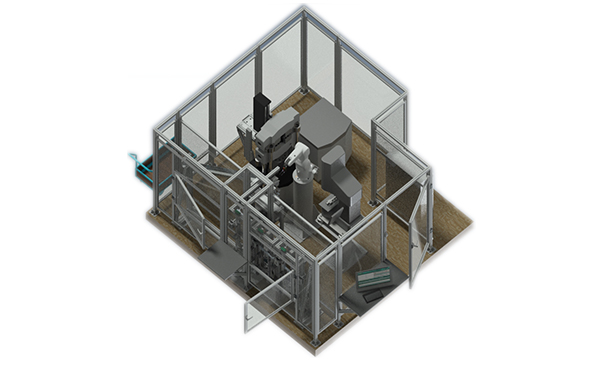
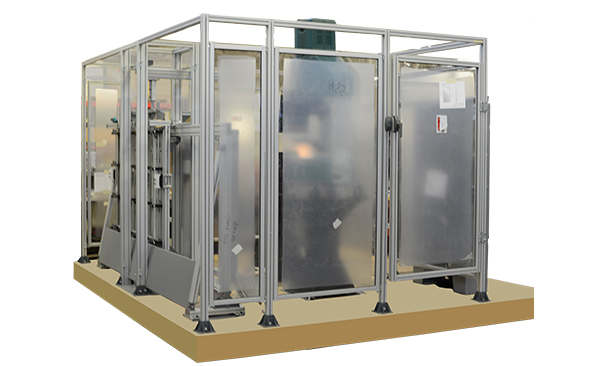
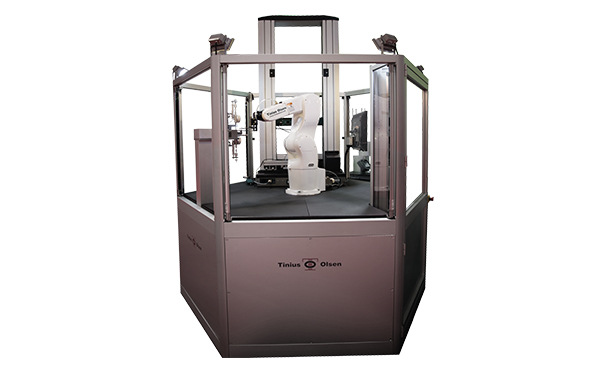
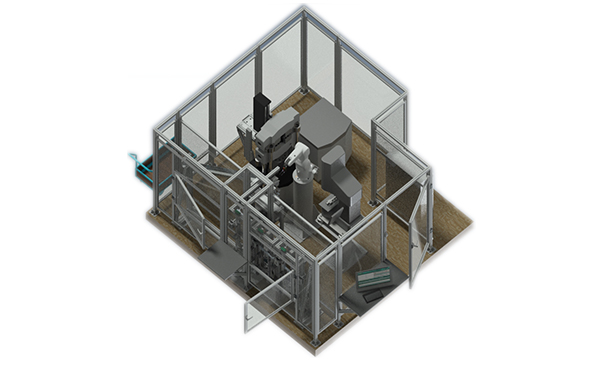
The key to the entire automated robotic testing system is that it can run without operator involvement. While this by itself has numerous advantages, it presents a possibility of a hazard to unfamiliar bystanders if the robot moves. To prevent any damage to operators and onlookers the entire testing system can be surrounded by polycarbonate safety shielding, with interlocked access doors and specimen loading doors to prevent any unauthorised access.
Automated Systems are built to accommodate your testing system be it housing a single machine or multiple machines, tensile, compression, flexural, impact, hardness, melt flow. The cell is impact resistant and transparent; it is interlocked with user and service password modes of entry.
The cell housing the automation system is configured with four specific objectives and capabilities;
● FOOTPRINT Optimize the footprint and envelope of the automation cell in support of productivity.
● SAFETY Transparent impact resistant panels give the user a clear a view of the system while providing protection from moving parts. Optional user recognition
for interlocked cell access for users and/or service personnel.
● ACCESS Light curtains in the cell panels allow people to operate safely while near the robotics.
● FLEXIBILITY The system is an investment in performance for many years, therefore the cell design and construction supports future repositioning if required.
-
Download User Instruction Manual
Please Fill the Fields to download pdf
-
Download Brochure
Please Fill the Fields to download pdf
- Request a Quote
Request a Proposal
Similar Accessories
330-012 3-Point Flex Test with LVDT
Short Beam 3-point Flexural Fixture
HT58 Lightweight Pneumatic Grips
Double Shear Bearing Strength Test - Procedure A
Single Shear Open Hole Bearing Test - Procedure B
Single Shear Bearing Strength Test - Procedure C
Compression Anti-Buckling Fixture
Shear Loading Compression Fixture
Specimen Identification Station
Combined Loading Compression Fixture
HT53 Miniature Knurled Roller Grips
V-notched Shear Compression Fixture
HF74 3-Point Wide Variable Flexural
Compression Cage for Environmental Chamber
122-007 Side operating Pneumatic Grip, 5kN