Testing > By Materials > Composites
Tinius Olsen
Composites
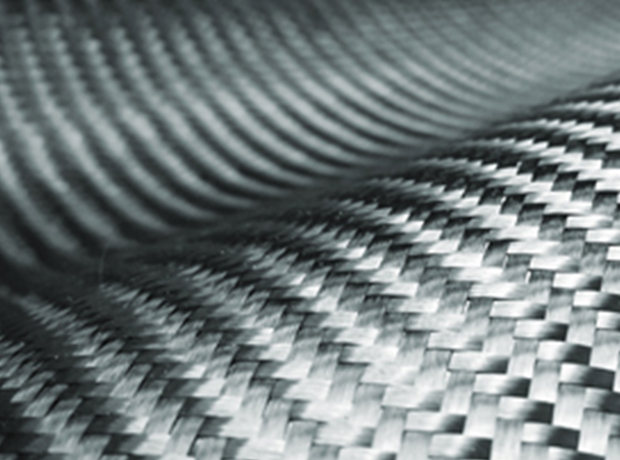
Composites are made from two component materials: matrix and reinforcement. Most composites use a polymer matrix material or resin. Reinforcement materials are often fibers but may be ground minerals. Typically, this results in a product containing 60% resin and 40% fiber, while vacuum infusion produces a product with 40% resin and 60% fiber. The strength of the final product is very dependent on this ratio. –
Composites are anisotropic and are characterized by Young’s modulus, shear modulus and Poisson’s ratio. Mathematics requires second-order tensors and up to 21 physical property constants. For orthogonal isotropy, there are three different physical property constants for each ratio – a total of nine constants to describe the relationship between forces/moments and strains/curvatures.
Designing and testing composites can be challenging. Common resins include epoxy, polyester, vinylester and shape memory polymer (SMP) resins. Common fibers include fiberglass, carbon fiber and Kevlar. Fiber-reinforced composite materials include short fiber-reinforced materials and continuous fiber-reinforced materials used in layered or laminated structures.
Types of composites:
- Thermoplastic resin composites, short fiber thermoplastics, long fiber thermoplastics and long fiber-reinforced thermoplastics
- Aramid fiber and carbon fiber in epoxy resin matrix
- Shape memory polymer composites are fabricated using fiber or fabric reinforcement and shape memory polymer resins as a matrix
- Reinforced concrete consists of loose stones (aggregate) with a matrix of cement with metal cables added for the tension of the concrete
- Metal matrix composites (MMCs) use metal fibers to reinforce other metals
Ceramic matrix composites (CMCs) are for fracture toughness, not strength. Applications include bone (hydroxyapatite reinforced with collagen fibers), cermet (ceramics and metals) and concrete. CMCs include asphalt concrete, mastic asphalt, mastic roller hybrid, dental composite, syntactic foam, mother of pearl and composite armor for military applications.
Engineered wood composites include wood fiber board, plywood, oriented strand board, wood plastic composite, pycrete, plastic-impregnated or laminated paper or textiles, Arborite, Formica and Micarta. Maleite also produces low weight, high hardness materials.
Composite lay-up designs involve treating the prepreg with various honeycombs or foams called a sandwich structure. This is a more common layup process for manufacturing radomes, doors, cowling and non-structural parts.
Since composites are used to improve rigidity and strength with a lighter weight, they are employed in critical applications such as military aircraft, commercial aircraft and aerospace where testing is especially important. The choice of fibers and matrices available and the ranges that can be made with blends enables a wide variety of properties to be incorporated. The best-known failure of ceramic matrix composites occurred when a carbon-carbon composite tile on the leading edge of the Space Shuttle Columbia’s wing broke on impact during take-off.
Request a Proposal