Building Trust Through Innovation in Materials Testing: LTI and Tinius Olsen’s Collaborative Journey
Introduction
In the world of materials testing, precision and reliability are paramount. Companies in high-stakes industries such as aerospace, nuclear, and additive manufacturing depend on advanced technology to meet rigorous standards.
Based outside of Philadelphia, PA, Laboratory Testing Inc. (LTI) has been at the forefront of materials testing for over 40 years, ensuring that its clients receive the highest level of accuracy and efficiency. Its long-standing relationship with Tinius Olsen has played a crucial role in fostering innovation, streamlining testing processes, and enhancing overall efficiency.
A Relationship Built on Collaboration
LTI’s partnership with Tinius Olsen is more than just a customer-supplier relationship — it is a dynamic collaboration. Over the years, LTI has provided valuable feedback to Tinius Olsen, influencing the development of new and improved testing systems.
As Mechanical Testing Manager Paul Szczepaniak from LTI shares, “Being part of the actual product development is an interesting experience. There’s a good back and forth between the companies, because we see what we need, and Tinius Olsen is always willing to accommodate.” (Figure 1)
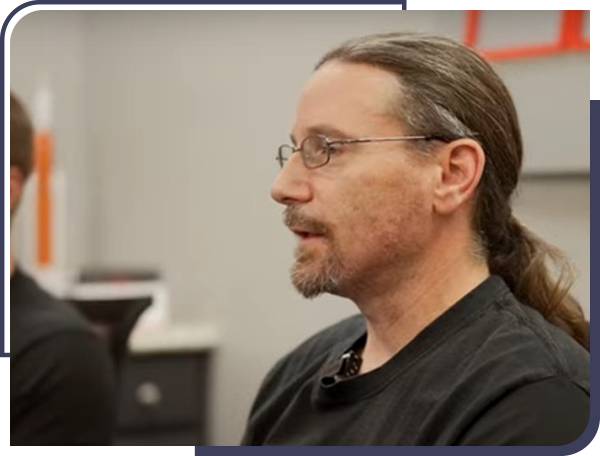
This direct engagement has resulted in tailored materials testing solutions that address real-world challenges, allowing LTI to optimize its operations, while contributing to the continuous evolution of Tinius Olsen’s technology.
Supporting Industries Through Innovative Solutions
To maintain an industry leadership position in the diverse range of industries it serves, LTI relies on sophisticated test systems that seamlessly integrate into its workflows. Tinius Olsen’s Horizon test system has been a game-changer for LTI, providing a streamlined and customizable platform that enhances data acquisition and usability.
“The ability to use that system and have it constantly updated has been invaluable,” says LTI’s Mechanical Testing Coordinator, Nathan Moyer. “Even if we request a specific feature, unless it’s an extremely complex demand, they generally implement it within a day or two.” This level of responsiveness and agility sets Tinius Olsen apart from its competitors, ensuring that partners like LTI can maintain its competitive edge.
Efficiency and Innovation with Non-Contact Extensometry
In high-volume materials testing environments, efficiency is key. LTI has significantly enhanced its operations with Tinius Olsen’s Vector Extensometer, which eliminates the limitations of traditional contact extensometers. The digital extensometer integrates adaptive AI capabilities with optical hardware to reduce test throughput times and complexity, automating the process of capturing strain and improving measurement accuracy, data consistency and operator safety. (Figure 2)
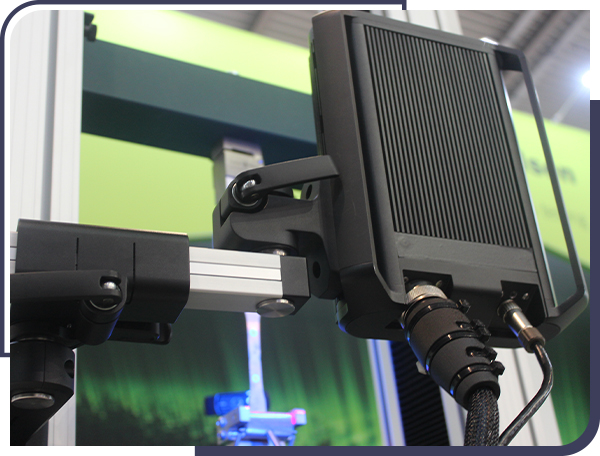
“Since it is non-contact, we could continuously run sample after sample and never have to re-verify the calibration of the extensometer,” Nathan explains. “And because it gives us digital, data-driven materials test processing, we have access to synchronized data in real-time, with virtually no lag.”
These advancements have minimized downtime, reduced costs, and improved throughput. The combination of Tinius Olsen’s precision hardware and sophisticated software has enabled LTI to optimize its testing processes like never before.
Reliability: The Backbone of Testing Operations
In a fast-paced and demanding industry, equipment reliability is non-negotiable. At LTI, almost every mechanical testing process involves a Tinius Olsen test system, from universal testing systems (UTMs) and hardness testers to impact test systems and melt flow indexers. Tinius Olsen systems form the backbone of LTI’s daily operations. This level of reliability ensures that LTI can meet the high standards required by its clients, while maintaining operational efficiency.
Driving Industry Innovation Together
Beyond advanced and innovative system offerings, Tinius Olsen’s active participation in ASTM standardization efforts further underscores its commitment to industry advancement. Paul shares, “If I receive a request from a customer that falls outside normal scopes, I can reach out to them and say, ‘Here’s what I’m trying to do. What can we do?’” This open collaboration has led to the development of custom instruments and unique testing setups that cater to LTI’s specific needs.
Moreover, Tinius Olsen’s commitment to swift customer support ensures that LTI experiences minimal downtime. “We just had a long-standing system go down, and Tinius Olsen had us back up in three days, whereas with another company, it could have taken weeks,” Paul highlights.
Conclusion
LTI’s decades-long relationship with Tinius Olsen exemplifies what true collaboration in materials testing looks like. Through constant innovation, responsive customer support, and advanced technology, Tinius Olsen has not only helped LTI optimize its processes, but has also played a pivotal role in advancing the materials testing industry as a whole.
For companies looking for a trusted partner in materials testing, the success story of LTI and Tinius Olsen speaks volumes. When precision, efficiency, and reliability matter most, Tinius Olsen delivers solutions that stand the test of time.
Hear it direct. Check out this video from Nathan and Paul at LTI about their experience working with Tinius Olsen.