3D Printing – Role of materials testing
Robotic exoskeleton technology has been with us for almost sixty years but the most recent advances in its composites base could see it being an integral part of missions to Mars in the 2030’s.
To many of us the term exoskeleton is reserved for the realms of science fiction or conjures up images of body armour clad superheroes such as Iron Man or even Batman. Although the vast majority of these have sprung from the fertile imaginations of artists and writers, the equally fertile lobes within the scientific community are turning this science fiction into science fact.
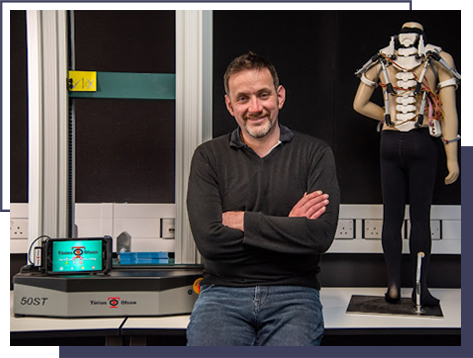
An exoskeleton is a rigid structure that wraps around the body and is often used to assist joint movement. This ‘exosuit’ try’s to act like an artificial muscle, aiding the wearers’ muscles to contract and extend.
The development of the first robotic exoskeletons can be traced back to around 1965, when General Electric developed the Hardiman, a large full-body exoskeleton designed to augment the user’s strength to enable the lifting of heavy objects.
The first exoskeletons for gait assistance were developed at the end of the 1960’s at the Mihajlo Pupin Institute, Serbia and in the early 1970’s at the University of Wisconsin-Madison in the US.
So, step forward Dr Matt Dickinson, Senior Lecturer in Mechanical Engineering at the University of Central Lancashire in Preston. Matt teaches in areas around concept design, with especial focus on the application of composite materials through 3D printing technology. Working out of the University’s new multi-million pound Engineering Innovation Centre, it appears he was in the right place at the right time.
“I’ll be honest, if you told me three years ago we’d be on the verge of developing world leading exoskeleton technology, I’d have questioned your sanity but here we are,” said Matt.
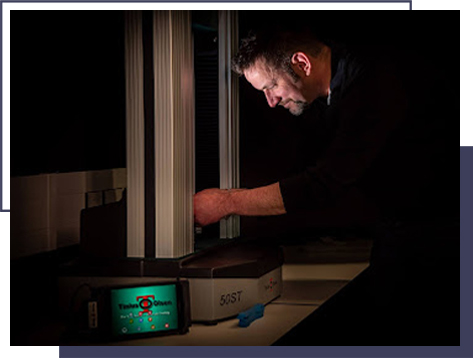
“It all started thanks to a local teenager who won the regional Primary Engineer competition back in 2019. Luckily, it was my responsibility to assess each entry and this one instantly struck a cord with me, as it simply asked why there is no special suit, or exoskeleton, that a child with muscular disease can wear to aid with mobility. To me, it was such an obvious idea that there must be one out there already but how wrong I was!”
The reason for this lack of development was purely down to design. For instance, how do you produce a suit that ‘grows’ with its host, is lightweight enough to be practical as well as being low cost and thus accessible to all?
“As a mechanical engineer, my first thought was to produce the suit out of aluminium, which looking back, would have been totally impracticable as well as being horrendously expensive to produce.”
The required material needed to be lightweight and accessible but it also needed to be affordable. In short, the technology would be impracticable if no one could actually maintain it, or if lower income families couldn’t afford it.
“The structure of the suit is what’s called a passive design system, meaning it’s part exosuit, which acts as a point of contraction, like a muscle but is also a passive exoskeleton, which distributes the force and load.”
“By taking these two approach’s we are attempting to combine both of these technology’s to build a hybrid system that will support the human frame and also aid in the muscle contraction and extension, which has led to the development of a new bespoke actuation method that we have designed.”
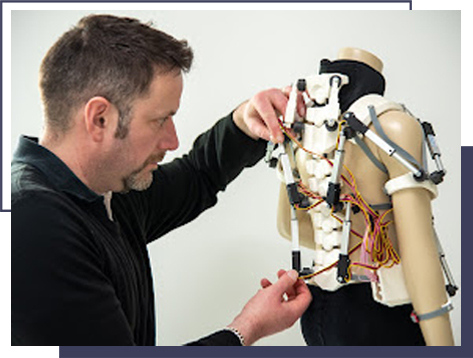
“The material I initially looked with the potential to support this criteria was polylactic PLA. At this point, nobody had tested the material to see if it was capable of supporting the human body but the results soon indicated we had hit on something extremely special.”
The first iteration of the design proved the suitability of the composite, although issues with the materials reaction towards UV light and the potential for the lactic acid in human skin to impregnate the material, needed to be addressed.
“Skin can sometimes activate the lactic acid within the material, which would see bacteria forming and ultimately compromise its structural integrity. This led us to incorporating a material embedded with copper nanoparticles, that creates a barrier between body sweat and the composite – a perfect anti microbial if you like,” said Matt.
The project is also exploring the use of chopped carbon PET. This is due to the extra strength the composite offers, which would be utilised as the core of the supportive structures of the suit, encased in poly lactic acid and carbon fibre.
“Basically, as with all projects such as this, things are continually under development. These are the materials we’re moving forward with at the moment but we’re continually looking to develop new composites that may supersede them,” continued Matt.
“At this stage we couldn’t move any further forward until we had a better understanding of the mechanical properties of these materials, which is where Tinius Olsen comes in.”
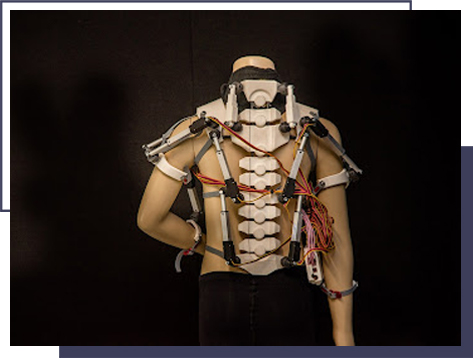
A chance meeting at one of the UK’s major engineering show set the scene for the working partnership, which has seen the company loan, initially, a 50ST testing frame, a platform for optical extensometry, load cells as well as the companies powerful Horizon testing software. Technicians are also on hand to give advice and direction where needed.
The partnership goes way beyond just machinery and advice however. Through Tinius Olsen, Matt was introduced to ASTM International, becoming Subcommittee Chair of the F48.04 Committee for standards in exoskeleton development.
“Primarily, what the ASTM F48 Committee are looking at, as with any R&D project that is going to be utilised with human use, is failure fatigue of the components that are being utilised. There’s also the life expectancy of the components and or material being utilised, through the usual compression, tension, and bending movements of everyday use. The Tinius Olsen machine and instruments we now have at our disposal will enable us to undertake this required testing at a much greater rate, literally taking years off the R&D time.”
“The doors this association has opened for the project are substantial, we have literally been catapulted from a lab in Preston onto the international stage, which has seen this development move forward exponentially. We literally wouldn’t have been able to get where we are currently without Tinius Olsen.”
“Our ultimate goal is develop a suit that can offer assisted living. It’s not really designed to give extra strength, more to give children with muscle disease more mobility, more independence and, most importantly, a greater quality of life.”
The suit will be going into human trials later this year.
Other Applications
It’s not just within the medical field this development can be successfully applied. As an example, space agencies such as NASA can adapt the technology into their spacesuit design for the forthcoming missions to Mars, planned for the mid 2030’s.
This can extend to military applications, not just supporting the body structure of soldiers and pilots but also ground crew and technicians responsible for the building and maintenance of heavy ordinance, tanks and aircraft.
Professional sport can also benefit. Protective body equipment for sports such American football and rugby are obvious applications but the opportunities for the supportive treatment of sports injuries are also substantial.
And of course the heavy lifting associated with construction and other manufacturing industries could see a reduction in work hours lost due to strain and back injuries to workers.
University of Central Lancashire, Engineering Innovation Centre
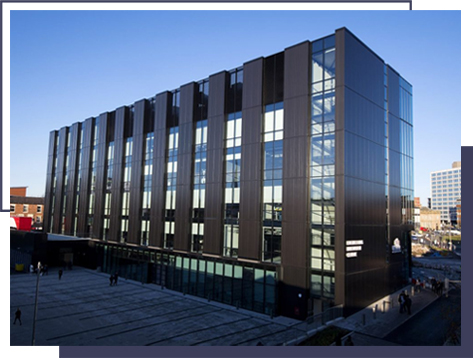
The Engineering Innovation Centre (EIC) of the University of Central Lancashire, UK is located on the Preston Campus, bringing together world-leading research, leading business minds and inspiring teaching in a spirit of collaboration and
discovery.
The new £35m EIC strengthens Lancashire’s position as a national centre of excellence for aerospace, advanced engineering and manufacturing and contributes towards maintaining the UK’s reputation as a global leader in these areas. It gives engineering students opportunities to work alongside research experts and industry partners, with the chance to work on vehicles inside our aerospace and motorsports laboratory, get to grips with flight simulators and drone technology, experiment with 3D printing, and a whole lot more.
The state-of-the-art teaching and research facility engages directly with industry and provides students with real-world experience on live projects. In doing so, the EIC acts as one of the driving forces behind the industrial strategy, both on a regional and national scale, addressing the need for innovation and producing the next generation of world-class engineers.
The Centre finds possible solutions to significant priorities in contemporary society and to elements of the UK Industrial Strategy.
Its role is to manage, support and stimulate strategic development and growth of engineering research and knowledge transfer, which will enable industry to address challenges at home and overseas. Activities are focused within a range of research areas containing a diverse series of specialist laboratories, covering a wide range of sectors including composites, oil and gas, 3D printing, intelligent machines, aerospace and motorsport.